
Amazon hit headlines around the world when it delivered its first parcel by drone in 2016.
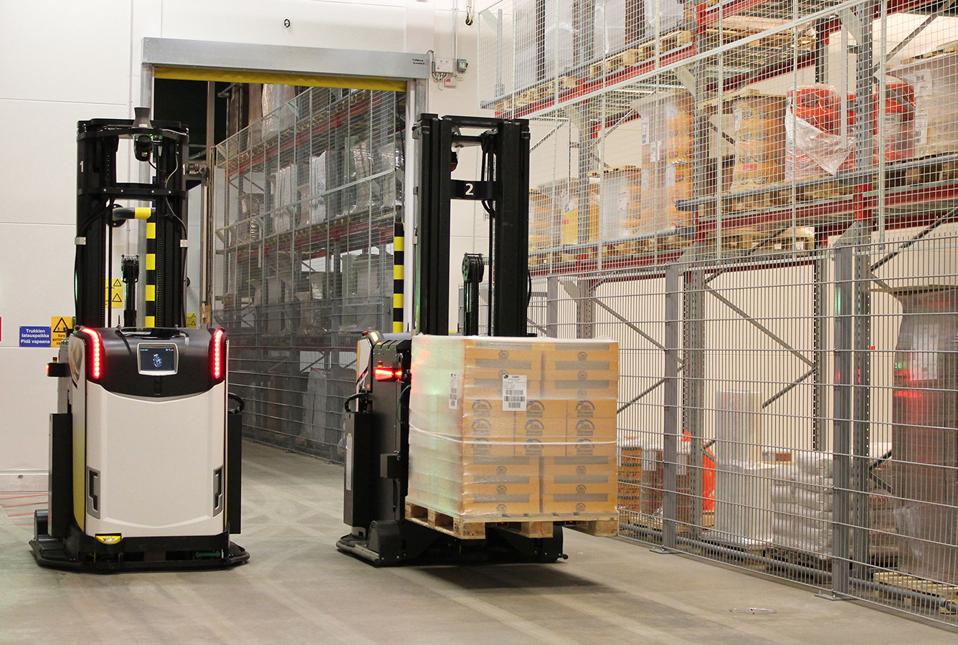
Automatic guided vehicles (AGVs) are still more common in warehouses than swarms of robots.
Today drone delivery flights are being tested around the world, training to drop off everything from medicine, to TV streaming sticks, to fast food.
But automated flights to customers’ front doors represent just the final step in a long journey, every part of which is increasingly automated.
Before goods can be flown by drone – or, more likely, delivered by courier – they must be selected and sorted in warehouses and logistics centers.
Automated forklifts
At its most advanced, warehouse automation can look like Amazon’s army of 100,000 robots that moves orders through its warehouses across the globe, or like UK online supermarket Ocado’s distribution center, where swarms of robots collect all the items requested by an online grocery shopper.
Automatic guided vehicles (AGVs) are still more common in warehouses than swarms of robots. These automated forklifts are nothing new; the world’s first automatic guided forklift was developed in 1971 by Nippon Yusoki, a predecessor of Mitsubishi Logisnext.
However, while early models moved along fixed routes across warehouse floors, guided by wires, today’s AGV technology can move across factory floors, guided by lasers, cameras or measurement of the surrounding environment.
Vehicles’ tracks contain certain virtual points along the route. When the vehicle arrives at any particular point, it requests its next move from the computer program overseeing organization of the warehouse, known as a warehouse management system (WMS).
Pallets, boxes or other items may be selected manually by humans, or by automated cranes and lifts that stack and unload the warehouse shelves.
Currently, AGVs are best suited for use in environments where repetitive travel and handling tasks dominate, and human labor might be put to better use in other areas. For smaller settings with more varied handling demands, a traditional, manually-operated forklift may still be preferable. While these dynamics will change over time, and AGVs will be able to handle a wider range of applications, manned forklift trucks are still in high demand. Thanks to the continued boom in ecommerce and a shift to cleaner electric vehicles, conventional forklift truck sales have reached unprecedented levels.
An electric trend
Research by Mitsubishi Logisnext shows that global demand for forklift trucks rose by 13.3 percent in 2017, compared to the previous year.
Customers’ concerns over carbon emissions mean that nearly two-thirds of forklift truck sales in North America are for electric vehicles, according to a report by the Industrial Truck Association (ITA) and Oxford Economics.
Advances in battery technology are helping to drive this mass adoption. Extending battery life makes it easier for operators to fit charging cycles around their production schedules. It can also help achieve a 10 to 15 percent increase in the volume of freight they can handle.
Digital warehouses
Sticking with a forklift operated by a human doesn’t exclude other opportunities for optimizing warehouses through digital technologies, however. When next-day delivery is the name of the game, having the most accurate stock inventory possible is critical.
Manufacturers and their supply chain are increasingly embracing software, often with machine-learning algorithms built in. These can learn everything from the time needed to produce any product, to the quantity required (so it’s ready just in time for delivery) to the optimal place to store that product in the warehouse.
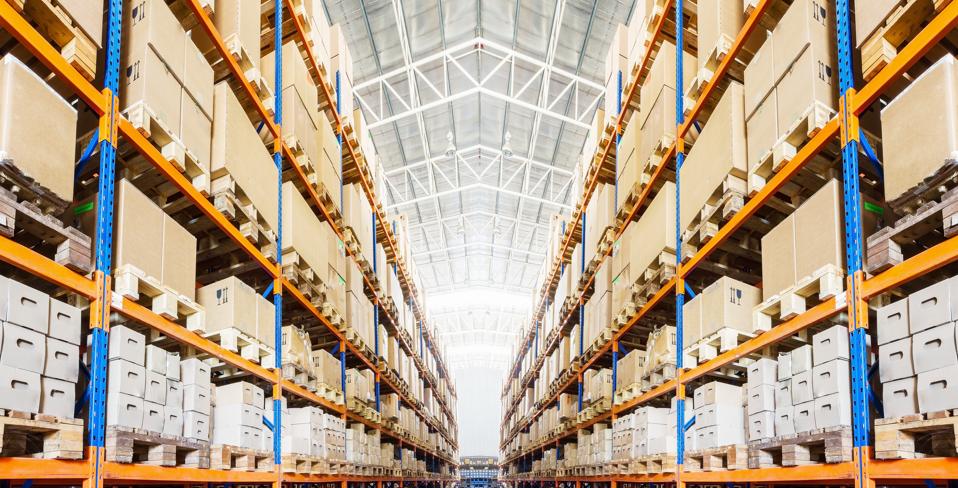
Advances in technology are revolutionizing the way products are being transported – from the warehouse floor, to your front door
In addition, digital tools that assist companies in optimizing their forklift and AGV fleets are on the rise. These include IoT-enabled applications to automate and simplify tasks ranging from service scheduling and dispatch to fleet management and centralized invoicing services.
As telematics and sensor technology continue to evolve, warehouse managers will see more predictive and proactive tools become available to them, enabling them to manage their fleets and keep goods flowing efficiently through their facilities.
And once goods leave the warehouse, fleet tracking capabilities monitor automated and human-powered vehicles, combining big data with sophisticated analysis to ensure consumers get their packages on time.
Drone delivery may seem like the future of logistics, but the reality is that today, across the world, humans and machines are already working together to get parcels delivered to customers in the fastest, cheapest and most environmentally-friendly way possible.
Source from : https://www.forbes.com/sites/mitsubishiheavyindustries/2019/02/15/from-the-stack-to-the-floor-how-the-logistics-of-warehouse-production-is-changing/#240d1b196bf9