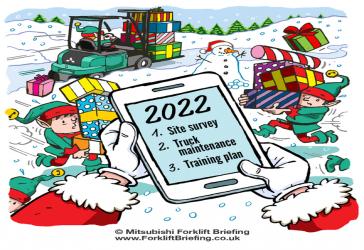
At time of writing, we may be in the middle of the busy Christmas period, but it’ll soon be the new year, and with it, time to make resolutions (and stick to them).
So here are a few suggestions for things that should be on your list:
1. Get a site survey
A thorough site survey should identify ways to make your operation more productive, flag any safety issues, and help you find areas where you can save money.
Everything on site from your equipment, to the racking and layout, to the site floor itself should be checked — rough surfaces are a major cause of wear to wheels, which could see you paying more for your maintenance contract.
And there are always ways you can be working safer. Does your site have adequate signage? Are your traffic routes well defined? Are there guard rails or other methods for pedestrian segregation? These are the sort of things that a site survey will look to help you address.
But a key thing to note is that it’s not just the what, but the who as well. Make sure your inspection is undertaken by a knowledgeable materials handling supplier who understands the needs of your business — they should be able to offer advice on what works specifically for you. A good supplier will reveal imminent threats to your business as well as any opportunities to maximise efficiency.
2. Stay on top of your truck maintenance
Unexpected breakdowns mean unexpected bills.
Forklifts can be complex machines and they’re often worked hard in tough environments for long hours. Parts can wear or break over time and lead to further issues if not caught right away.
Daily checks are your first — and best — line of defence against breakdowns. Ensuring your operators stick to a simple routine before using the truck enables any problems to be caught early on. A reputable forklift maintenance specialist can recommend a series of daily, fleet and annual checks for your site.
If you undertake repairs in-house, make sure you use mechanics who have been properly trained in forklift truck maintenance. They will need to use high-quality, approved spare parts to avoid unpleasant surprises.
3. Look at your training plan
Continuous training is paramount for a safe work environment. Take time to examine your training plan and see if more should be done. It’s not enough to just do initial training when staff join — when was the last time your operators undertook refresher training? Have any elements of their job changed since they started that require further training?
And ensure you check that whoever is conducting the training has been fully assessed and accredited to industry-recognised standards.