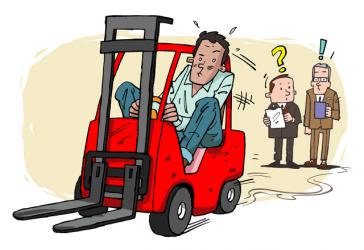
Over the last few decades people have been getting bigger, and that includes fork lift operators. But are forklift designers including that in their calculations?
Over the last few decades people have been getting bigger, and that includes fork lift operators. But are forklift designers including that in their calculations?
A changing population means an on-going need to redefine what we think of as ‘the norm’ in the workplace.
Forty years ago, the average shoe size was two sizes smaller than it is today. Where once a size 12 or 13/46 or 47 would be unusual, they are now on the shelves of most shoe shops.
It’s just one example… but is typical of the changes that must be considered when designing and building lift trucks. If people are growing, then their working space must grow around them.
But what does that mean for forklift trucks?
Taking the average
You’d think designers would simply calculate a new “average”… but that simply won’t work.
When the US Army designed its first standardised aircraft cockpit in 1926 they based it on the average measurements of male pilots (height, weight, arm-length etc.). But the knock-on effect was that they then needed to select pilots who most closely matched the exact criteria for ‘averageness’.
Fast forward to the Second World War and the same cockpit plan was still in use. However, with many more pilots being recruited, a large number of deaths occurred during training because the restricted dimensions of the cockpit hindered the ability of many pilots to control their planes.
Post-war research found that less than 5% of pilots fitted the ‘average’ across just one third of the 10 dimensions in use. As a result, the US Air Force (as it had become) began designing adjustable seats, pedals etc… Pilot performance improved dramatically.
Are you sitting comfortably?
The benefits of proper ergonomics in the work environment — be it a fighter plane, a forklift, or an office desk — can be pronounced.
A 1990 study testing subjects working in an ergonomically optimised setting found a 17.5% increase in productivity compared with those working in poorer environments.
A similar study in 2003 found a 17.7% increase in productivity when participants were given a highly-adjustable chair and proper ergonomic training.
But how can you apply this to forklifts?
A better cabin
In order to accommodate today’s larger operator, the cabin needs to be not only larger, and genuinely supportive but must also fully adjustable in many different ways.
With models such as the EDiA EX 80V electrics and SENSiA reach and multiway reach trucks, Mitsubishi designers carried out extensive research across the whole of Europe in order to deliver the highest ergocentric outcomes.
The results are clearly reflected in every aspect of the truck designs. Operators’ compartments are the largest on the market and are accessed via wide, low steps (essential in locations where drivers must get on and off the truck frequently throughout the working day. Importantly, and unlike almost every competitor, Mitsubishi cabins ensure drivers of every size are wholly contained within the truck itself – minimising the risk of limbs being trapped between the truck and racking.
Suspension seats are adjustable to accommodate the wisest possible range of body types and provide excellent back support and encourage good posture while working.
In may forklifts the operator’s arm is under-supported but, since they represent around 10% of our bodyweight, they too need careful consideration. Failing to deliver sufficient support can put a strain on the upper back, shoulders and neck. Over time this can result in RSIs (Repetitive Strain Injuries) or permanent skeletal damage.
That’s why Mitsubishi has devoted so much design effort into the armrests for its EDiA EX and SENSiA models. Fully adjustable, they ensure excellent support from palm and wrist to elbow and upper arms. What’s more, the units are equipped with fingertip controls that have won international awards for their ease of operation.
Our conclusion?
It seems likely that body shapes will continue to change – something designers will need to accommodate, not only to preserve the well-being of operators but to maximise productivity.
- Action points
- Investigate the ergonomic options of trucks and ensure operators – are fully contained and protected within the confines of the truck
- Offer drivers ergonomic training
- Contact your local dealer
Source: https://forkliftbriefing.com/increase-productivity/the-growing-problem-of-larger-operators/